The Brain behind the Electric Powertrain
The Brain behind the Electric Powertrain | Focus on the Motor Controller and Software
A combination of the motor controller and software are integral to the FRIWO Electric Drive Train because each of the components such as the battery pack and the brushless DC motor require a good brain to get the best out of them. Like a person, the better the brain, the more intelligent it is and the more capable that person is of completing a task, the same could be said with the drivetrain!
We have focused a lot on the battery packs and the brushless DC motor of late but the real hero is the integration between the motor controller and the software, the capabilities that they offer and I want to focus on the brain within this blog.
So, what is the Motor Controller?
The motor controller is the black circular device that can be seen mounted on the motor above.
This device does exactly what the name would suggest... Control the Motor!
Operating at 48V, this device was specially developed for use in light electric vehicles. With a continuous output of 6kW and a peak power of up to 12kW.
Thanks to the automatic teach-in function, the controller forms a powerful unit with the motor within a very short time.
Our field-oriented control system with highly efficient control algorithms then ensures a unique driving experience.
A combination of the motor controller and software are integral to the FRIWO Electric Drive Train because each of the components such as the battery pack and the brushless DC motor require a good brain to get the best out of them. Like a person, the better the brain, the more intelligent it is and the more capable that person is of completing a task, the same could be said with the drivetrain!
We have focused a lot on the battery packs and the brushless DC motor of late but the real hero is the integration between the motor controller and the software, the capabilities that they offer and I want to focus on the brain within this blog.
Key features
Safety and reliability
What’s more is that the motor controller recognises malfunctions that may occur during operations and will shut down quickly deciding whether to tune down the power so not to damage the system.
Size Vs Power Rating
Best in class and can be installed almost anywhere on a electric vehicle allowing installation in tight spaces on vehicles such as electric scooters, quad bikes, or even Go-Karts.
Flexible
Will control and manage any 3 phase brushless DC motor, equipped with digital hall sensors.
Grid Compatible
Will manage 40 battery packs in parallel increasing overall capacity.
Proven Performance
The motor controller and software was used for a high pressure pump in the Porsche LMP1 during 24hr race of Les Mans.
What Are the Software Capabilities?
This intuitive piece of electric vehicle software can be configured by the user to deliver exacting performance depending on the user requirements.
For example if you run a fleet of Go-Karts and in the morning you have a children’s party booked you can create a profile setting parameters to limit speed and torque in order to make the go-kart child compatible and then you can set up a separate profile perhaps to increase speed and torque, whilst adjusting braking for the adult group booked in later. After initial setup, this operation is a simple toggle between profiles via a button or on the app.
Or you could have a fleet of scooters and need to conserve battery power as much as possible so the need to maximise running time. There are combinations of parameters that can be set to achieve this so let’s say you need to ride your vehicle over a distance and you know it is mainly downhill you could actually set up a profile to re-coup energy and put this back into battery to give you additional running time and what’s more is that profiles can easily be selected using the app making the system straightforward to access and manage.
Should you edit parameters that result in a negative effect on the behavior of the controller then the safety element kicks in and these commands are usually intercepted or parameter changes are limited to safe values. Without drilling too much into the software set up and listing every tab and every parameter I have included the image above to highlight the interface once logged in, and the start-up is very straight forward as you move along the top tabs, selecting parameters as necessary from a selection of options, inputting values ranging from 0-100 in some cases or 1-10 in others.
Applications
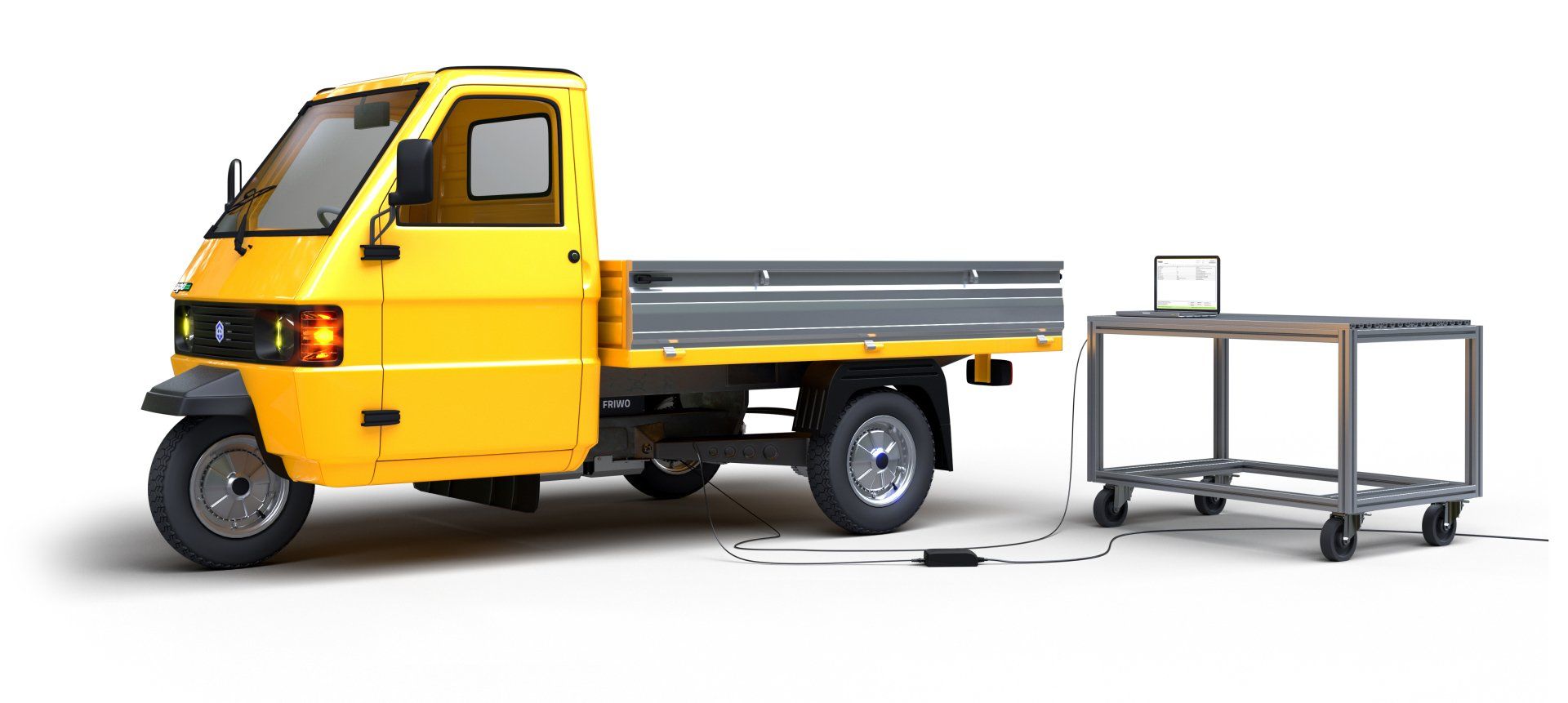
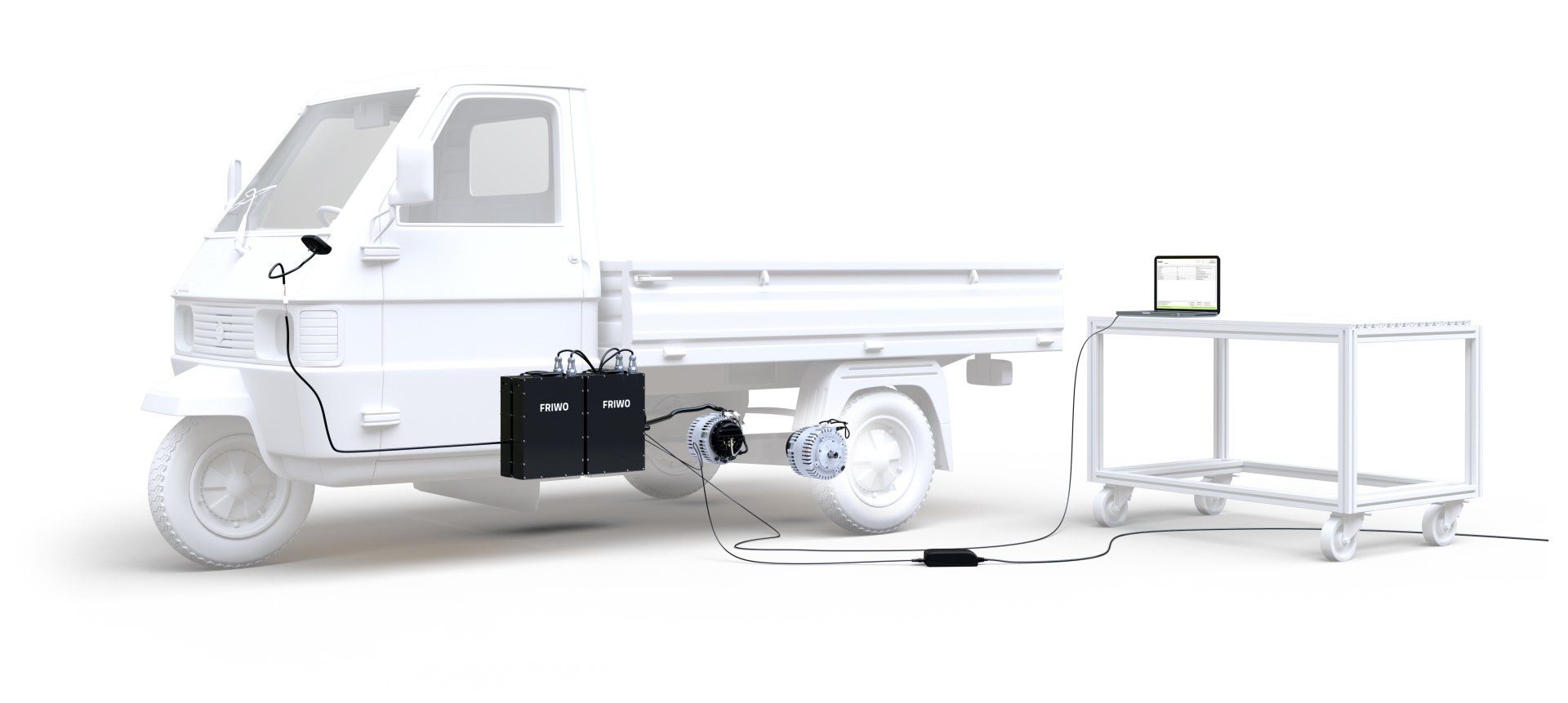
There are many applications that the FRIWO Motor Controller and Software can power and I have mentioned the obvious ones above but the system is very flexible and was recently selected to solve an issue with a large water pump used with an external motor and the problem was that the flow needed to be limited. The motor in its current state was generating too much power and therefore the pump was running too quickly. The motor controller was implemented, parameters were set up and the motor was limited to a specific speed, reducing the speed of the pump.
Other applications include e-bike, scooters, Rickshaws, Quad bikes, Golf carts, Drones, Conveyor belts, Stairlifts and quite frankly, any application that requires a motor and there needs to be an element of control.
To conclude, the combination of the FRIWO motor controller and software is integrated to fine tune any battery and motor combo and will be the brains of your application to offer the flexibility to meet ever changing requirements.
Found something of interest?
Contact Us!
While you're here, why not read some of our other blog posts?
We are sure you'll find something interesting!
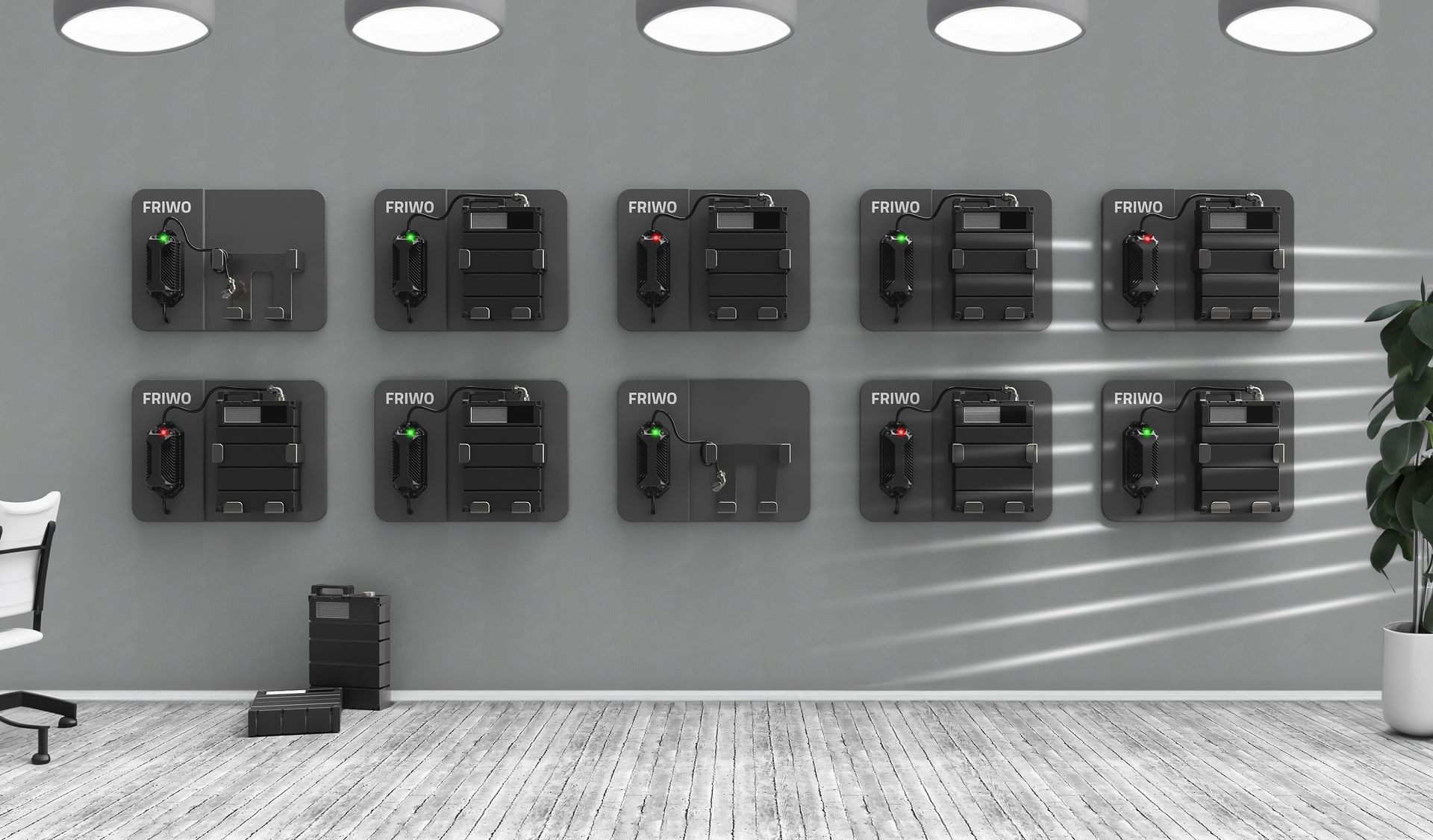
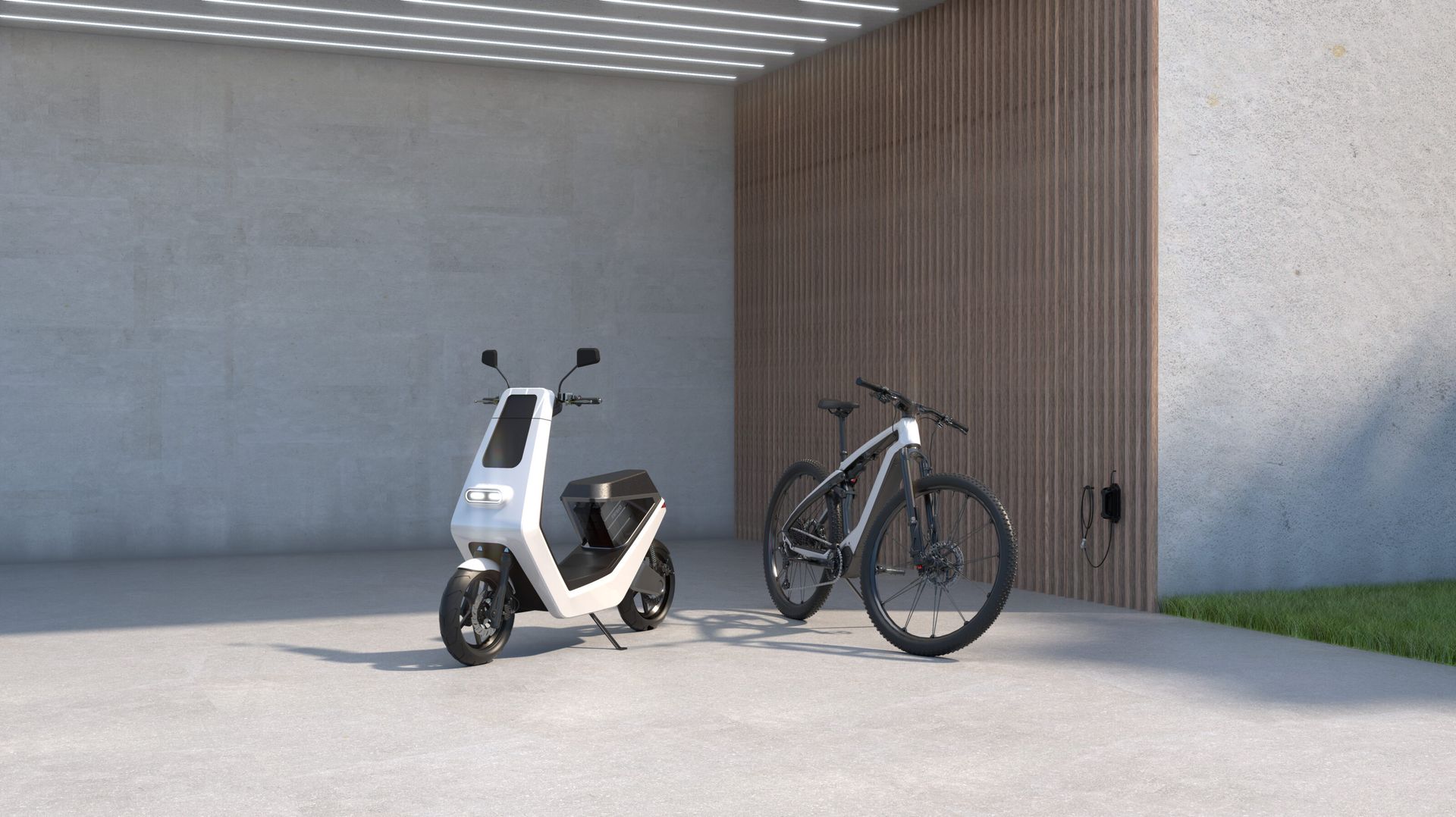
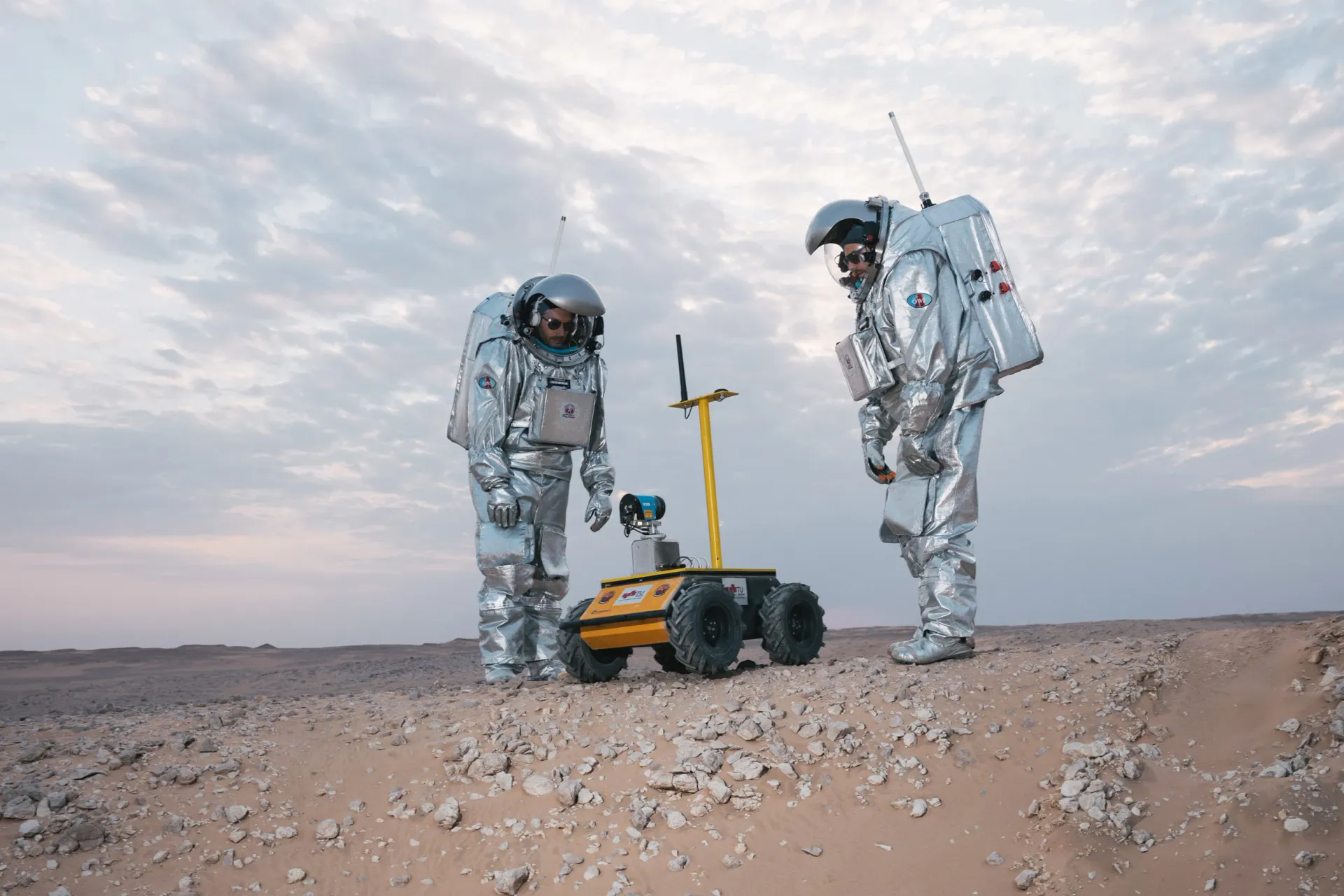